13 Simple Ways to Improve Employee Safety
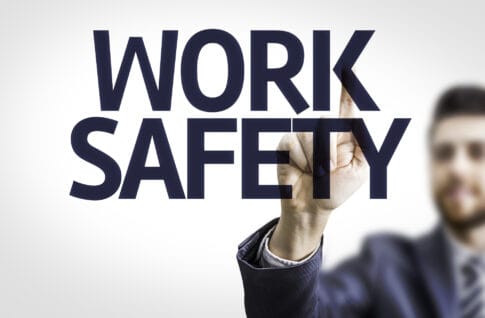
No matter how hard you try, there’s no such thing as a perfectly safe workplace. Did you know that there are over 340 million workplace accidents and 160 million victims of work-related illnesses every year worldwide?
Even though it will never be perfect, we should always strive to improve, as these numbers are truly chilling. Fortunately, there’s plenty you can do to improve the safety of your workplace. Here are some employee safety tips to use in your organization!
1. Train Employees About Workplace Practices
What are the biggest dangers in your workplace? While it varies between industries and jobs, the most common include:
- Heavy lifting
- Tripping and falling hazards
- Heavy machinery (saws, planers, belts, etc.)
- Sharp objects
- Blunt and moving objects
- Human accidents
- Close working spaces
- Fumes and other toxic materials
There are plenty of other examples that may apply to your enterprise. There are too many ways a person can hurt themselves in any workspace to make it 100% safe. However, training your employees on how to properly use or navigate these safety challenges will go a long way.
For example, teaching employees how to properly lift heavy objects, operate machinery, and navigate through a close working space can do a lot to improve workplace safety overall.
Moreover, this also includes how employees interact. This includes announcing yourself when walking behind someone, informing others about safety practices, and more. The more safety training employees take, the better.
2. Keep Employees Alert
Do you have a fast-paced work environment? If so, encourage employees not to come to work when they are feeling sick or otherwise unprepared for a full day on the job.
Beyond that, the most important thing you can do is offer breaks. This is especially important in warehouse or factory settings. If workers are left to work for too long, the chances of an incident increase dramatically.
The more frequent these breaks are, the better. Instead of offering a 20-minute break, consider offering two 10-minute breaks, or even more if possible. Eight hours or more of the same task will lead to greater human errors.
Also, employees should be encouraged to stretch during their breaks. Light stretching is incredibly effective at preventing injuries during manual labor, and it can even help prevent long-term conditions for people working at sedentary desk jobs.
3. Have Well-Trained Staff On-Site
Having well-trained safety staff on site, and preferably in every department, is very helpful. Not only can they help other employees perform their tasks more safely, but they can also potentially handle an emergency situation.
We aren’t suggesting that all of your department heads become EMTs. Instead, they can easily obtain some OSHA certifications or first aid/CPR certifications.
Beyond that, there’s also bloodborne pathogens training, hazardous materials training, and more that may apply to your enterprise. See which workplace safety trainings are available for your employees.
Also, ambulances can take time to arrive, especially during the winter. If your budget allows for it, your emergency plan can even include having a medical professional on-site. Not every organization can afford this, but it could potentially save lives.
4. Keep the Workplace Clean
Unsanitary workplaces pose more health risks, and cluttered workplaces pose more safety risks. It’s very important that employees and management are aware of the safety standards in their departments. You should also hold them to account for maintaining these standards year-round.
This is especially important during the Covid-19 pandemic, which is still a persistent threat, regardless of people’s attitudes toward it. Nearly three years in, 335 Americans are still dying every day from Covid-19, which is expected to increase throughout the winter.
It isn’t just Covid-19 now, with variants of the cold and flu spreading at unprecedented rates. Fortunately, with the right planning and preparation, you can keep your employees safe from these threats. Check out our Covid-19 resources to see how you can prepare your workplace.
5. Provide (and Maintain) Proper Ventilation
Even in a warehouse setting with no machines, ventilation is still essential. Toxic fumes from delivery trucks, heating systems, and more can pose health risks to you and your employees.
Not only do you need proper ventilation, but you need to use and maintain it. Ventilation only helps when it’s turned on and when it remains clean.
Generally, you should have commercial ventilation systems serviced every three to five years. However, if you have a business that uses gas, coal, or other fossil fuels to power machines, then we’d recommend doing this every one to three years or as needed.
The reason for the increase is that these fumes can quickly lead to buildup, and the consequences could potentially be lethal to employees. These fumes carry carbon monoxide, which is extremely poisonous and kills up to 500 people each year while hospitalizing over 50,000.
6. Provide Personal Protective Equipment
Personal protective equipment (PPE) is essential in many jobs, especially for preventing the spread of Covid-19. However, it’s also essential for preventing employees from breathing in toxic fumes, preventing the spread of bloodborne pathogens, and more.
PPE will include different materials depending on your industry and equipment. However, high-quality masks and gloves are a good start.
If employees show up to a job and don’t anticipate needing these materials, why would they have them? Providing them yourself is critical for overall health and safety.
7. Have Safety Equipment On Site
Beyond PPE, it’s important to have emergency first aid kits on site, preferably within 100 feet of every worker. Having staff or managers trained in first aid is also essential for this.
For larger networks of employees, we also recommend having an AED machine available, as well as someone trained in CPR/AED in every department.
Moreover, this safety equipment also includes emergency exits, visible exit signs, visible evacuation routes, and more.
8. Have Emergency Plans in Place
Beyond simply having the right equipment, it’s important to have the right procedures in place. Your management team (and preferably employees) need to understand these procedures and practice them. These plans include:
- Evacuation routes
- 911 procedures (when to call, clearing for an ambulance, etc.)
- Specific emergency procedures (threats of violence, fires, etc.)
- Response teams for specific situations
- Heat advisory procedures
Of course, there are plenty of other examples that may be specific to your enterprise. Regardless, it’s better to have these plans and not need them than to need them and not have them! The sooner you can respond, the better.
9. Encourage Employees to Care For Themselves
Employees should not feel obligated to come to work when they are sick or when they do not feel up to the job. If anything, the opposite is true.
Instead, employees should feel encouraged to care for themselves when needed, both in and out of work. This includes having sick time but also taking a step away from their work when they aren’t feeling well. For all you know, this could prevent someone from heat stroke or even cardiac arrest.
Remember that your employees are competent adults. They can care for themselves under most circumstances, so give them the freedom and tools they need to do so, and make sure they report when an incident occurs.
10. Have Employees Report Incidents
Employees should understand the phrase “when in doubt, fill it out.”
Incident reports are an essential part of employee health and safety. Employees or managers should fill out reports whenever incidents happen, no matter how minor. Not only will this help you keep track of incidents for legal purposes, but it can help you make more informed decisions for employee health and safety.
For example, if you notice that 30% of your incident reports involve cuts on workers’ hands, then you may choose to invest in puncture-free gloves. These reports can help you visualize and understand the most serious hazards in your workplace, which will only help make it safer in the long run.
On top of that, it’s also important to keep an open dialogue with employees. This is especially true when it comes to potential hazards.
You can easily incorporate a classic “suggestion box” or encourage staff to speak up about possible hazards that could pose safety risks to them or their fellow employees. They know the job better than anyone at the management level, so hear what they have to say about safety issues!
11. Enforce Safety Rules
If you see a violation, enforce the rule. If your managers see a violation in their respective departments, they should do the same.
There are plenty of ways to enforce this that are company-specific. You can give verbal warnings, written warnings, and more. If employees repeat the same behaviors, then you can require them to retake their safety training.
Alternatively, you can also use positive reinforcement to help facilitate a safer workplace. For example, some companies offer rewards to their teams for going a certain period without any workplace accidents. You could also have management praise or give merit to employees who follow the safety guidelines, make safety a factor in raises or bonuses, and more!
Overall, we recommend using a combination of both of these strategies. Workers don’t want demerits or a reputation for being unsafe employees, but at the same time, safety isn’t always a glamorous feature at work. As an employer, you have the power to change that.
12. Lead By Example
You and your management team should always lead by example. If managers regularly violate safety rules and protocols, you should expect your workers to do the same. Always ensure that your managers are held to either the same or even a higher standard than employees when it comes to safety.
Also, the more knowledgeable your management team is, the more they can pass along to your workers. Management should have more extensive training for emergency procedures, OSHA compliance, and more.
13. Promoting Employee Health
A lot of employee safety comes down to employee health. The healthier your staff is, the less prone they will be to accidents and injuries. The good news is that you can facilitate this yourself.
For example, offering your employees health resources and encouraging them to stay hydrated can go a long way. You could also host health challenges like weight-loss challenges, water drinking, quitting smoking, and more.
Hydration, nutrition, and exercise will do a lot to limit workplace hazards. This is especially true when it comes to reducing:
- Heat exhaustion or heat stroke
- Cardiac arrest
- Joint-related injuries
- Stress fractures
- Lifting injuries
- Tripping and falling hazards
The list goes on. Employees who follow best health practices are simply less likely to face injuries on average. Some simple steps you can take include:
- Providing clean drinking water in every department
- Offering nutritious snacks on-site
- Offering employees healthy living resources
- Adding gym memberships to your benefits package
- Conducting a voluntary health assessment
Again, the list goes on. Remember to treat your employees like the adults that they are, but there’s nothing wrong with encouraging healthy lifestyles!
Employee Safety Is the Top Priority
Safety is not “a” top priority, it is the top priority in any work environment, which is why it should always take precedent when planning new business practices.
Now that you know some employee safety tips, put them to use. A safe workplace is a productive workplace that attracts and retains talented employees. Facilitating a safe and healthy workplace is beneficial to everyone involved, especially the business owner.