How to Improve Hazardous Materials Communication in the Workplace
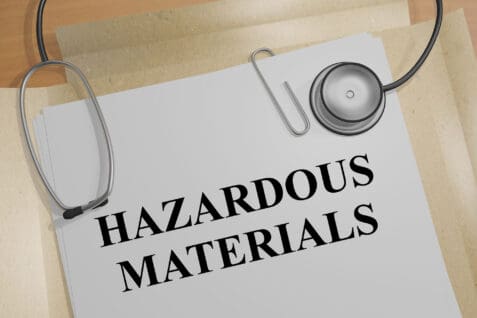
Back in 1972, the US government estimated that 25 million workers were exposed to at least one of 8,000 different hazards.
But here’s the most shocking part: For 90% of those hazardous materials, neither the employer nor the employee could identify them in the products they worked with.
The good news is that things have improved a lot in 50 years. Companies now have strict HazCom training programs in place to ensure their employees stay safe. In nearly every industry, this training is required by law.
Is it time to focus on HazCom improvement in your workplace? Here are four tips that will help.
1. Create a Written Plan
You don’t want to “wing it” when it comes to hazardous materials. In fact, OSHA requires that all employers have a written hazardous communication plan on hand and accessible. Your plan must specify your procedures for labeling and maintaining SDSs, as well as providing employee information and training.
If it’s been a while since you updated your plan, start with a complete inventory. Identify every hazardous material in your workplace and check the latest manufacturer recommendations. Read every label and record all relevant details into one document.
2. Use Proper Signage & Symbols
Signs and symbols transcend language and leave no room for misunderstandings. They’re essential if your employees speak different languages but they’re still invaluable even if everyone speaks the same language.
For example, a skull and crossbones symbol is immediately recognizable on any product label.
Make sure that every potential hazard at your workplace has a label that includes:
- a product identifier
- pictograms
- signal word
- hazard statements
- a precautionary statement
- contact information for the responsible party
You can use an online SDS system to create custom labels that are in full compliance with current regulations.
3. Maintain Current Safety Data Sheets
Next, contact your chemical manufacturers for the latest up-to-date information on each product. Request as SDS if you don’t automatically receive one from your supplier.
If you choose to maintain your SDSs electronically, OSHA requires that you have an adequate backup system in case there’s a power failure, equipment malfunction, or another emergency.
Most importantly, your safety data sheets must be readily accessible to your employees at all times.
4. Provide Ongoing Employee Training
Every employer must train their employees on the hazardous chemicals in their work specific area. This needs to be done before their initial assignment and any time new hazardous materials are introduced.
This training must be given in a language that the employees can understand. Each worker must also be aware of all protective measures that are available throughout the worksite.
HazCom Management for Hazardous Materials
Thanks to the latest HazCom regulations, employers and employees can enjoy a safer workplace with fewer hazards. If you see the need to make improvements to your hazardous materials communication, use the tips above to guide your efforts.
KHA is here to help make your job easier (and your workplace safer). Our online SDS service gives you access to the latest safety data sheets, regulatory reports, and custom label development.
Contact us today to learn more.