What Are the Main Causes of Workplace Accidents?
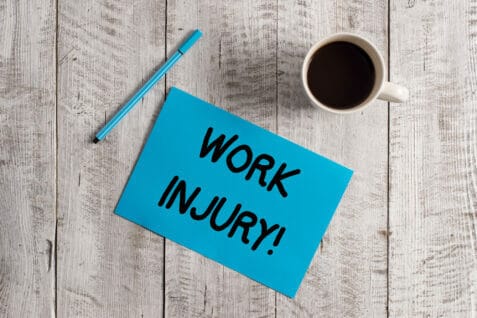
Each year, millions of individuals across the globe are involved in accidents that occur within the context of their employment. It is estimated that approximately 2.3 million individuals worldwide are affected by workplace-related accidents annually.
When it comes to workplace accidents, prevention is key. A workplace injury can result in lost productivity, lawsuits, and even fatalities. As an employer, it’s your responsibility to create a safe work environment. To do so, it’s vital to understand the main causes of workplace accidents.
By identifying the causes, you can take steps to prevent them from occurring. In this article, we’ll explore the most common causes of workplace accidents. We’ll also provide tips on how to prevent them.
Let’s crack on with this! Here are the common causes:
Human Error
Human error is a multifaceted issue. It may be the leading cause of workplace accidents.
It is often the result of a combination of factors. Such factors include a lack of training, fatigue, distraction, or simply not paying attention to what you’re doing.
For example, an employee may forget to turn off a machine before cleaning it, resulting in a severe injury. Human error can also be caused by overconfidence and a lack of experience. Or it can be about insufficient knowledge of safety protocols.
You should note that human error is not always intentional. It is often a result of unintentional actions or omissions that lead to accidents.
It’s important to understand that accidents caused by human error are not always the fault of the employee. They can often be the result of the circumstances surrounding the accident.
Human Error Prevention
To avoid mistakes, employers can do a few things to make sure their workers are supervised well. They should give proper training to employees about how to use equipment and follow safety rules. This training should be continuous and updated when necessary. The reasoning is so that workers know about any new safety procedures.
As well, employers can encourage employees to take breaks when they’re feeling fatigued. This can help to prevent accidents caused by lapses in attention or concentration.
Employers can also implement policies that require employees to report any safety concerns or hazards straight away. This will help make sure that hazards are identified and addressed before they lead to accidents.
Supervision is also crucial in preventing human error. Employers should ensure that supervisors are well-trained and have a clear understanding of safety protocols. Supervisors should also be responsible for monitoring employee behavior. They need to take action when necessary to prevent accidents.
Unsafe Work Conditions
Unsafe work conditions are a prevalent cause of workplace accidents. This can have severe consequences for employees and employers alike.
Unsafe work conditions can arise from a variety of factors. These may include:
- Inadequate maintenance
- Lack of training
- Failure to carry out proper safety procedures
One example of unsafe work conditions is poorly maintained equipment. Equipment that is not properly maintained can pose significant hazards to employees.
This can result in accidents that can range from minor to severe. For instance, a worker operating machinery that’s not maintained may suffer injuries from broken parts.
Another common factor contributing to unsafe work conditions is inadequate lighting. Poor lighting can make it difficult for employees to see potential hazards.
This may lead to slips, trips, and falls. It can also make it challenging for workers to do their jobs in an effective manner.
Preventing Unsafe Work Conditions
To prevent accidents due to unsafe work conditions, employers must prioritize regular inspections and maintenance of equipment. This includes identifying and repairing existing hazards. But also includes ensuring that employees are trained to recognize potential hazards.
Regular maintenance can also help to prevent equipment failure. It will reduce the likelihood of accidents.
Providing proper lighting is another essential factor in preventing accidents. Employers should ensure that all work areas are well-lit for specific tasks. Proper lighting can help employees to see potential hazards and avoid accidents.
Furthermore, ensuring a clean and hazard-free work environment is crucial in preventing accidents. Employers should take steps to regularly clean work areas. They should remove any debris or hazards that could cause an accident.
Plus, implementing proper safety procedures is a must. We’re talking about things such as wearing personal protective equipment.
Chemical Injuries
Chemical injuries are severe and potentially life-threatening forms of workplace injuries. They are caused by exposure to hazardous chemicals. These injuries can range from chemical burns to respiratory problems.
Such injuries can occur from direct contact with a chemical or inhalation. They can also happen via ingestion.
Prevention
To prevent chemical injuries in the workplace, employers must prioritize proper training on the safe handling and storage of chemicals. Employees should receive adequate training on the proper handling of hazardous chemicals.
They should provide instructions on how to use personal protective equipment (PPE). We’re talking about things such as gloves, goggles, and respirators.
Employers must also ensure that all chemicals are properly labeled. They should make sure employees understand the meaning of each label.
Proper storage of chemicals is also essential in preventing chemical injuries. All chemicals should be stored in a safe location. And also kept away from heat sources or other potential hazards.
Employers should also ensure that all chemicals are properly sealed. Also, employers should make sure that they are not mixed with incompatible substances. If such chemicals are mixed, they can result in a dangerous chemical reaction.
Emergency Response Planning
In addition to these preventive measures, employers should establish an emergency response plan in case of a chemical injury. Employees should be trained on the steps to take in case of exposure to hazardous chemicals. This may include first aid measures and reporting procedures.
Regular inspections of chemical storage areas and equipment are crucial. Employers must ensure that all equipment is in good condition.
They should also regularly monitor the workplace environment. Plus, employees should look for potential hazards and address any identified issues right away.
Lack of Care for Employees
A lack of care for employees is a significant issue that can lead to workplace accidents. When employers do not focus on the safety of their employees, accidents will happen.
This can happen when an employer does not provide adequate training. Or if they fail to provide necessary safety equipment. Or if they neglect to enforce safety policies.
To prevent accidents due to a lack of care for employees, it is essential to focus on employee safety. This can start with providing proper training to employees. By doing so, you ensure they know how to use equipment safely and avoid potential hazards.
Providing necessary safety equipment is also crucial. They will reduce accidents caused by a lack of protective gear.
Enforce Safety Policies
Enforcing safety policies is equally important. The reason for this is to ensure that employees understand the consequences of unsafe behavior.
It’s essential to communicate these policies regularly. And to make sure that all employees understand them.
Regular hazard assessments can also help identify potential risks. The result may be you prevent accidents from happening in the first place.
As well, employers should strive to create a positive work culture that values employee safety. When employees feel valued and supported, they are more likely to prioritize safety. They may also avoid risky behavior.
Having open channels for feedback can also help identify areas where safety measures can be improved.
Practical Tips for Managers to Create a Culture of Safety
Creating a culture of safety in the workplace is not only important for the well-being of employees but also essential for the success of a business. As a manager, you play a critical role in promoting safety in the workplace.
Here are some practical tips for managers to create a culture of safety:
Lead by Example
One of the most effective ways to promote safety in the workplace is by leading by example. As a manager, you should model the behavior you want to see in your employees.
This means following safety protocols and wearing personal protective equipment. It also means reporting any safety concerns promptly.
Provide Adequate Training
Proper training is critical in preventing accidents caused by human error. As a manager, you should ensure that your employees receive adequate training on the use of equipment and safety protocols.
Training should be ongoing and updated as needed. This way you will ensure that employees are aware of any changes in safety procedures.
Encourage Open Communication
Encourage employees to communicate any safety concerns or hazards immediately. This will help to ensure that hazards are identified and addressed before they lead to accidents.
As a manager, you should create a culture of open communication. This is a culture where employees feel comfortable speaking up about safety concerns. If employees are afraid to speak about such things, it might mean serious safety concerns are left unchecked.
Employees should be involved in safety initiatives to increase their commitment to safety. As a manager, you should encourage employees to participate in safety committees, safety audits, and safety training sessions. This involvement can help to promote a culture of safety and increase awareness of safety issues.
Regularly Inspect Equipment and Work Areas and Provide Adequate Resources
Regular inspections can help identify and address hazards in the workplace. As a manager, you should prioritize regular inspections of equipment and work areas. These inspections can help to identify hazards, such as faulty equipment or inadequate lighting, that can lead to accidents.
To promote safety in the workplace, you should ensure that employees have access to the resources they need to stay safe. This may include personal protective equipment, safety training, and hazard reporting systems. Adequate resources can help to prevent accidents and promote a culture of safety.
Recognize and Reward Safe Behavior
Recognizing and rewarding safe behavior can help reinforce a culture of safety in the workplace. As a manager, you should acknowledge and reward employees who follow safety protocols and report hazards promptly.
This recognition can help to promote safe behavior and encourage others to do the same.
Risks for Employers if They Don’t Follow Health and Safety Laws
Employers have a legal and moral obligation to prioritize the health and safety of their employees. Failure to follow health and safety laws can result in significant risks for employers.
One of the most serious risks is legal action. This can result in fines, lawsuits, and even criminal charges.
Legal action can also damage a company’s reputation. This may make it more difficult to attract and retain employees and customers.
Failure to follow health and safety laws can also lead to workplace injuries. These incidents can have a significant impact on the physical and emotional well-being of employees. They can also result in lost productivity, increased absenteeism, and high turnover rates.
This can result in additional costs for employers. We’re talking about medical expenses, workers’ compensation claims, and lost productivity.
Employers who fail to focus on health and safety may also struggle with low employee morale. Employees who feel unsafe or unsupported in the workplace may experience stress, anxiety, and reduced job satisfaction. This can lead to decreased productivity, increased absenteeism, and higher turnover rates.
Also, employers need to maintain good safety sheet data management practices. This way they stay compliant and legally in business.
Causes of Workplace Accidents Explained
Workplace accidents can have devastating effects on employees, employers, and their families. As such, preventing these accidents is crucial.
Employers must focus on employee safety by identifying potential hazards. They should then address them and provide a safe work environment for their employees.
At KHA, we offer safety data sheet (SDS) management. We’ve been offering our expertise in SDS management since 1985! If you wish to learn more about what we can offer, contact us here.