GHS Labels: Common Mistakes to Avoid in Chemical Labeling
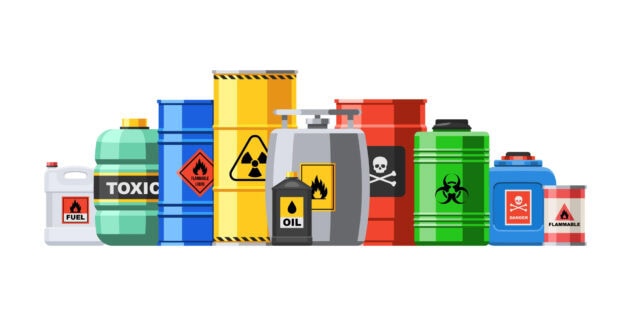
As reported by Worldmetrics.org, human error accounts for around three-quarters of all incidents and errors in the chemical industry. Even common chemical labeling errors can lead to significant safety and compliance concerns, resulting in actual harm to employees, if not fines, and a range of sanctions. So, how do you avoid the most common issues in this business area and keep your people safe?
Read on to discover and learn about many of the most common mistakes one can make during the GHS label application process. Consider implementing all the GHS compliance tips below to avoid penalties and maintain a safer work environment. By the end of the article, you will also discover how KHA’s latest software solution can help you get your GHS labeling right and safeguard your employees.
Inadequate Hazard Communication Practices
The Globally Harmonized System of Classification and Labelling of Chemicals (GHS) is a United Nations effort to ensure all businesses use the same chemical labeling methods.
Training in this system is crucial for everyone at a company. For this reason, the phrase “Those employees didn’t know” does not enable businesses to avoid accountability.
At every stage, you must clearly communicate chemical hazards to ensure workplace safety and comply with regulations. OSHA’s most recent set of standards is very explicit about what you must do in this step and a highly relevant resource to help you get on the right track.
Ensure that this communication occurs not only in the location where these chemicals might be but across all departments. Every person should be able to leverage the latest Safety Data Sheets (SDSs) and have received training in what they state. One of the best ways to do this is via an electronic SDS system that automatically updates, ensuring everyone has seamless access to the best information.
Overlooking Update Requirements
GHS regulations state that you must regularly update labels to comply with worldwide standards. Neglecting these can lead to any hazard information you have being outdated, whereas the most up-to-date details will likely safeguard your workforce better.
Either implement regular reviews of your GHS labels or use an electronic system to track electronic and manual audits automatically. You can also ensure you update the information available to all employees faster using a digital tool, avoiding further safety risks.
Misinterpreting GHS Label Pictograms
A misinterpreted GHS pictogram can cause employees not to understand all the details about a chemical hazard. This mistake can lead to accidents as the worker mishandles the material, causing potential damage, injury, or death.
Ensure your training standards include regular updates to employee knowledge and training audits to ensure people know what pictograms mean. Studies from the Journal of Safety Science and Resilience (September 2024) show that such training reliably improves pictogram retention.
Educational resources and easily referred-to tools should also exist due to the fallible nature of human memory.
Incorrect Label Size and Placement
All labels should be easily read by those using them. As such, the labels should have the correct:
- Print resolution
- Size
- Placement location
- Ink and color
All these elements ensure that you reduce risks by making the labels as simple to comprehend as possible. So, source a high-quality label printer to adhere to any requirements related to safety labels.
UN chemical label regulations do not require these labels to be a specific size. However, consultancy firm Croner-i confirms that if you need to work with EU companies, it is a mandated requirement of the bloc. Also, if litigation occurs, a court is unlikely to consider hard-to-read labels as a reasonable method of warning your employees of potential dangers.
Incorrect Hazard Statements
While it may seem obvious, you need to ensure you place accurate statements on your labels. In addition to making sure you use the latest information, as listed above, having a single, reliable source of information is also very useful.
Among other good safety labeling practices, the following is an excellent checklist to ensure you have the latest hazard statements on display:
- Consult the latest SDSs
- Cross-check these with GHS classifications
- Check for consistency from different sources such as OSHA and the UNECE
- Use the exact phrasing provided by the GHS
- Verify the details are accurate for combined mixtures
- Consult with any local regulatory updates
Please note that this list is not exhaustive, and you may need to take additional steps to ensure compliance. A digital tool from KHA can often help you with this process, connecting to a central source offering only the most up-to-date data.
Missing Supplier Information
Neglecting or misplacing supplier information will cause compliance issues for you whether things to wrong or not. It can also hinder emergency response efforts if there is any potential of contamination at any part of the supply line.
As such, ensure you list the mandated supplier information on GHS labels. If possible, use a central database to manage this, ensuring you print out the right data with each delivery.
Failure to Include Supplemental Information
Supplemental information is any other safety details you may need to communicate beyond basic GHS requirements. These may be uniquely relevant to your industry, business, or location.
Make sure you have strict guidelines on what supplemental information you need and adhere to that at all times. Using label printing software will also give you a way to ensure this information ends up on all labels automatically.
Easily-Damaged Labeling
Any labels you use must be able to withstand the conditions the chemical container will undergo. This fact is also true of a label or sign in a location where you store or utilize the chemical.
Investigate options such as laminated or coated labels, and ensure the labels are clear enough to maintain legibility even when slightly damaged. You can then respond to any damage long before it becomes a problem.
Ensure Compliance and Safety with KHA’s Solutions
Now you know the labeling mistakes to avoid, it’s time you took action. KHA offers solutions that allow you to adhere to SDS and GHS label requirements from various oversight organizations. We offer standardized templates, integrated training resources, and easily-referred documents to help everyone at all levels of a business.
So, avoid costly fines and potential harm with KHA’s comprehensive information and labeling software. Schedule a demo with us to learn more about what we offer and invest in a reliable compliance tool to secure your company’s future.