How to Assess and Respond to Environmental Risk Factors
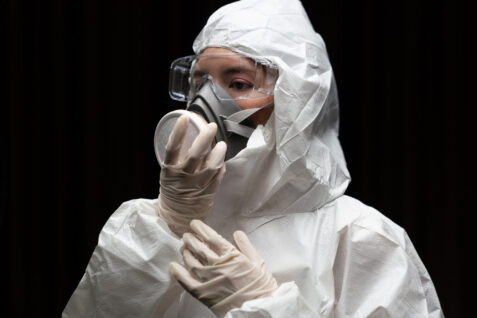
The US government continues to offer several key guidelines on recognizing and responding to risks in your business, including environmental risk factors. However, many organizations struggle to keep up with risk assessment tools and processes and often continue to use outdated, non-compliant processes. As such, they may often suffer from a lower level of safety than other businesses, risking reprimands, fines, or worse from organizations such as OSHA, not to mention litigation.
Read on to learn how integrating advanced online platforms can help you streamline your risk or hazard assessment processes, allowing you to respond to problems or emergencies easily and quickly. So, read on to discover how to transform your environmental hazard strategy and stay ahead of the curve today.
Identifying Environmental Risk Factors
There are several potential environmental risk factors you could fall victim to during your business processes. Examples of these include:
- Chemical spills
- Toxic emissions
- Air contamination
- Water contamination
The more chemicals you utilize in your role, the more likely these are. As each of these could potentially impact the health of your workers, the general public, and the wider environment, it is crucial to avoid causing any issues by following key regulations.
Identifying these hazards andir release could impact your surthe surrounding areao identifyiassessings they pose.
Methodologies for Identifying Specific Risks
When attempting to discover specific risks within your business, you can use techniques such as:
Systematic checklists to ensure that every part of your business’ process receives equal review with every audit. Having key elements checked every time can help discover and capture issues that you might otherwise easily overlook or which are hard to notice due to size or other factors. Having a checklist can also help with training, as it means all employees have access to the same steps, removing the need to learn how to return to the same level of oversight.
Risk mapping looks at all the data you have as a business related to your business risks and charts them. As such, they are easier to visually link together, allowing you to see risk clusters where you might need to focus or areas you have not previously considered.
Fortunately, OSHA and EPA recommendations are both based on the idea of helping businesses respond to the possibility of risks. By following their specific regulatory criteria, you can identify where you should improve your processes and in which areas you might need to document your efforts to ensure ongoing auditing.
Walkthrough surveys are a method of ensuring the assessor directly interacts with the environment in question. Instead of simply asking whether specific areas follow safety criteria, an assessor can observe the specific elements they are responsible for and report on them from a position of greater knowledge. Assessors can also interact with workers directly during these periods and receive context and insights they would not receive if they only interacted with automated systems.
Utilizing Safety Data Sheets in Assessments
SDS are documents your team can use to communicate key information about chemicals they utilize, including:
- Chemical properties
- Correct hazardous material handling
- What to do if the chemical leads to an emergency
- How to respond to personal harm caused by the chemical
They act as an essential reference for preventing potential environmental impacts by providing key information on the best ways to store and move the chemicals.
With a digital SDS management system, such as that provided by KHA, you can automate both the updating and retrieval of these SDS, ensuring greater accuracy over time. Doing this means they can act as an ongoing training tool for your employees, boosting hazard awareness and safe handling processes in the business. They will also communicate to those engaged in risk assessment the potential risks that handling the chemicals can create and how to handle many of them.
Complying with OSHA and EPA Recommendations
Regulatory body OSHA demands that employers conduct regular assessments of hazards in the company. They offer safety compliance guidelines, such as their Process Safety Management Standard 29 CFR 1910.119, which dictates how to evaluate potential failure and consequences when handling chemicals. This information can be a key starting point when creating your risk assessment.
OSHA standards are not only a recommendation, as US law requires adherence to many of their regulations. As failing to follow these can lead to fines of up to $165,514 per violation, it is essential to ensure that you pay attention to them.
Similarly, EPA offers recommendations that outline risks management processes you can use to evaluate environment and health risks in your company. They offer specific criteria, such as:
- Emission thresholds
- Exposure limits
- Required steps for monitoring
- Methods for testing
- Hazmat safety strategies
These can help you to pinpoint further risks that could cause significant issues for you as you continue to work with chemicals.
Mitigation Strategies in Environmental Hazard Management
There are several steps you can use to ensure you prioritize and respond to environmental hazards. You should document these so that your employees can take appropriate steps every time. They include:
Defining risk priority reasons based on severity and likelihood to ensure greater risks to your company, its employees, and the environment see focus first.
Develop control measures for reducing risks through:
- Fixing problems
- Eliminating assets from processes
- Substituting assets
- Offering more or fewer controls to employees
Each of these can offer you more precision in how your company can respond to issues.
Emergency preparedness and ontingency processes, from fire drills, to training individuals in responding to emergencies, can give you a greater responsiveness to issues that appear during the course of work.
Empower Your Safety and Risk Strategy with Key Insights
Both planning for and responding to potential environmental risk factors ensures that you are ready to comply with protocols and standards at any time. One of the best ways to do this is to use a digital documentation process to ensure your team have all the information they need at any point.
KHA offers this through its KHA Environment software, as well as other offerings. We can ensure you have all the tools you need to handle any issue as it appears. So, get in contact for a demo and learn what we can do for your team moving forward today.