Better Job Safety Analysis
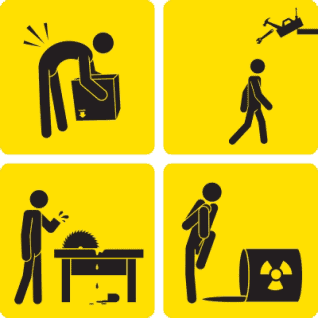
The Job Safety Analysis (JSA) reduces risk by assessing hazards at each step in the procedure, helping identify both the appropriate PPE needed as well as steps to mitigate hazards.
In addition to helping plan for safe work, JSAs are a key tool for areas like reporting, investigating near-misses and employee training. It’s important to get it right, given how often these forms are used.
Here, we give you some strategies to improve your JSAs to reduce workplace risk and help you get the most from your EHS management software.
1. Ask the Right Questions: As you break the job into its sequence of steps, look at each individual movement to identify hazards or potential hazards accompanying each step. Obviously, it’s important at this stage to dig deep, pointing out every conceivable hazard a worker might encounter.
To fully identify hazards, begin with questions like:
- Could a worker strike or be struck by an object?
- Is it possible to get caught within or between objects?
- Are there any slip, trip or fall hazards?
- Will any of these actions (pulling, pushing, bending, lifting) strain the worker’s body?
- Do any hazards threaten a worker’s body parts, such as hands, feet or eyes?
- What equipment is nearby? Does it present any additional hazards?
Be sure to include not just hazards associated with the task itself, but also those present in the general work area, like rotating pulleys, belts or blades.
2. Get Feedback: You can’t create a JSA in a vacuum, and it won’t be effective unless someone who understands on-the-ground conditions helps create it. Seek out team members who understand the process in question and can help you identify its inherent hazards.
You should also get feedback after you’ve completed the JSA, testing it out with employees who can help you identify any gaps. For the best results, be sure to remind employees you’re evaluating the safety of the procedure, not the individual’s performance of it.
3. Dig Deeper: If you run into a complex process or an area you don’t understand well, the worst thing you can do is to check the boxes without investigating further. Instead, find ways to dig deeper. Is there an employee who understands this process better? Are there similar procedures that can provide insight?
For complex processes involving multiple steps, tasks, movements and hazards, some safety professionals turn to photo or video. This allows you to review the details at your own convenience, rather than feeling like you have to complete it on the spot, which can lead to errors.
EHS management software can also help with Risk Management by incorporating risk tables at each step of the JSA, as well as by giving you a risk ranking for the procedure as a whole.
4. Stay Involved: Many organizations call in third-party consultants to help with their safety programs. It’s simply a way of life for large companies, where complex processes and high-risk outcomes call for outside experts getting involved with JSAs.
One mistake to avoid with outside consultants is taking a hands-off approach, giving over the reins and assuming the expert is equipped to go it alone.
Instead, you need to stay involved when consultants are involved in creating JSAs. That’s because it allows you to provide practical input to the document, also building your understanding for better performance once the consultant has left.
5. Keep It Updated: At the end of the day, a JSA is a living document. Processes are rarely static, and any time a job procedure changes or a new one is introduced, the JSA needs to be updated to reflect that.
In Conclusion
A JSA isn’t a guarantee that work will always go safely, or that incidents will never occur. Learning how to create better JSAs, however, is something you can count on to improve workplace safety.