Essential Guide to HazCom Compliance for Workplace Safety
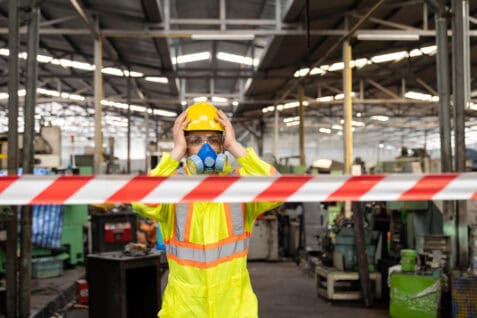
The Occupational Safety and Health Administration (OSHA) works hard to ensure workplaces across the country comply with specific safety standards while using chemicals.
However, understanding HazCom compliance can be extremely challenging for newer businesses and even established businesses that don’t have a comprehensive safety program. Fortunately, learning the basics of Hazcom and the tools you need to get and stay organized will move you in the right direction.
Read on to learn everything you need to know about HazCom compliance to ensure your workplace follows appropriate safety measures.
What Is HazCom Compliance?
HazCom is a communication standard from OSHA designed to protect people from chemical illnesses and injuries. It provides employers and employees with the information they need to recognize and evaluate various chemical hazards and take action.
This communication standard also revolves around the fact that people have the right to understand the types of chemicals they’re working with and what types of injuries they can cause.
You can find this type of information via safety data sheets (SDS), employee training, and chemical labels. The information comes from hazard determination, which is a process of evaluating all available scientific evidence to determine if a chemical is hazardous.
Manufacturers mostly conduct these determinations, but distributors and employers can also conduct determinations, especially if there are concerns about the chemicals in use.
Why Is HazCom Important?
Proper HazCom helps your business avoid expensive penalties for not following proper safety protocols. HazCom can be challenging, and in 2023, HazCom violations were the second most common reason for citations.
Therefore, the number one goal of HazCom is to improve workplace safety by continuously finding new ways to enhance hazard communication. It also helps each employee understand what chemicals they’re working with so they can better understand why these safety measures are in place.
What Are the Basic HazCom Requirements?
HazCom focuses on workplace safety measures and specific hazard communication standards. The requirements for this process include:
Create a Hazard Communication Program
First, your business needs to have a written hazard program that communicates how you plan to keep employees safe.
This program must outline the procedures and policies for handling different hazardous chemicals. It should also inform employees of all the potential health risks that might occur from improper handling. You must also create a custom plan for your organization to address your specific needs and form a plan for regular updates.
If you don’t have a solid hazard communication plan, it’s best to sit down and create an outline. You should start with a list of the hazardous chemicals your employees have to work with and then dive into the details.
Keep a Chemical Inventory
Keeping an accurate chemical inventory is crucial to creating a solid hazard communication program and is what you’ll base the scope of your program on.
OSHA requires safety professionals to keep an accurate inventory of all chemicals present in the workplace, which allows emergency responders to find the information quickly. Chemical inventory should be quick and easy to access and contain essential information like:
- Product name
- Manufacturer’s name
- Manufacturer’s address and phone number
- Identification marker
Any consumer products like non-hazardous materials don’t need to be inventoried. You should also separately track biohazardous materials and radioactive waste under a separate inventory program.
Maintain Safety Data Sheets
Remember, keeping a proper chemical inventory means you need accurate safety data sheets. Effective SDS management starts with understanding the process, including health and environmental risks.
A safety data sheet (SDS) contains essential information about each chemical, like its properties, protective measures, and safety precautions for storing, handling, and transporting. The SDS also includes the properties of every chemical, along with physical, environmental, and health hazards to be aware of.
SDS sheets contain 16 sections, which include substance and supplier identification, hazard identification, ingredient composition, and more.
Due to this, online SDS management is critical for building a system that accurately stores and updates chemical hazard information. It also allows you to have remote access, making it easy to update the system when you need to. You also won’t have to worry about losing critical information.
Label All Chemical Containers
You must properly label all chemical containers, which includes any secondary containers you use for mixing chemicals. These labels, known as Globally Harmonized System (GHS) labels, are part of a global system of classifying and labeling chemicals.
The labels ensure employees understand the hazards associated with the specific chemical they use. Labels compliant with HazCom should include:
- Product identifier which is the name of the chemical
- A signal word that identifies the level of danger like “warning”
- Hazard pictograms which are pictures showing the hazards of a specific chemical
- Hazard statements that outline the exact hazards
- Precautionary statements include a set of instructions to help people protect themselves
Finally, chemical labels should also contain supplier details like the name, address, and phone number of the company you’re ordering from.
Provide Regular Chemical Safety Training
Finally, HazCom requirements involve proper training for every employee to make sure they know how to safely deal with hazardous chemicals. All training should take place before a new employee starts work and when you introduce new chemicals.
The training includes various topics like how to detect harmful chemicals and the outcomes of unprotected exposure. Employees will also learn about company protocols, labeling systems, chemical inventory management, SDS management, and OSHA compliance tips.
Finding a professional company is one of the best ways to facilitate chemical safety training for your organization. For example, KHA offers comprehensive HazCom training along with Hazmat inventory training, online SDS management, and more.
Improve Your HazCom Compliance Today
Remember, HazCom compliance for your business doesn’t have to be complicated. You can turn to Kelleher, Helmrich, and Associates, Inc. (KHA) for all your HazCom needs.
KHA offers 35 years of experience serving distributors, manufacturers, healthcare facilities, and many other industries. We offer a wide range of services to help you improve employee safety protocols like SDS services, SDS mobile app, hazardous material inventory, and more.
We can help you meet OSHA safety regulations while staying on budget with no hidden costs. Make sure to contact us today to learn more about our services.