How Often Should We Do a Chemical Risk Assessment?
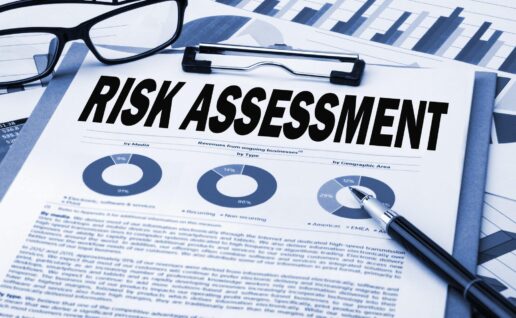
In the United States, around 20% of small businesses fail within their first year. There’s no shortage of causes behind this occurrence, but one of the most notable is the failure to implement safety procedures.
Even a single incident can be catastrophic and lead to major issues, such as injury or the violation of industry standards. Companies that handle chemicals must regularly conduct a chemical risk assessment to maintain safety.
However, not everyone understands how often they should do so. Let’s explore the key information you need to know before moving forward.
How Can Chemicals Be Harmful?
There’s no shortage of ways the chemicals at your facility can be harmful. Major risks include:
- Causing health issues for employees
- Dangerous chemical reactions
- Death or injury from toxic chemical exposure
Many chemicals can cause substantial damage to the victim, even through brief or mild exposure. Certain health issues won’t manifest until after long periods have passed.
For example, people who develop mesothelioma often do so after years of exposure to asbestos, which is often present within insulation. Proper inventory control and management are essential for minimizing risk. This generally involves securing chemical containers and accounting for all chemical agents.
What Does This Test Entail?
There are numerous steps involved when properly assessing chemical risk. Understanding them beforehand will allow you to prevent mistakes from occurring. Listed below are the most important to keep in mind.
Take Inventory
Before moving forward, you’ll need to take inventory of the chemicals at your facility. As long as your chemical containers are properly labeled, this shouldn’t be an issue.
You should then organize this list by job roles and activities. It’s not uncommon for roles to involve the handling of multiple chemicals, and this information is important to document.
Identify Potential Hazards
The number of hazards you deal with will vary depending on the chemicals you work with. The number of chemicals you handle will also play a role. It’s best to check two or three times to assume you didn’t overlook potential hazards.
Determine Exposure
Assess the level of chemical exposure your employees experience. Doing so provides valuable insight into how at-risk people are in your organization. Not all exposure is apparent, so you should thoroughly examine your procedures.
Control Chemical Risks
After identifying the risks present at your company, you should make an effort to control them. This involves putting safety measures in place to prevent certain situations from arising.
If you can’t eliminate the chemicals, you should look to replace them with less hazardous or non-hazardous chemicals. One of the most common scenarios involves replacing hazardous paints with products that don’t contain as many harmful chemicals. If you can’t adjust the chemicals you use, you should improve your employee training and procedures.
It’s crucial to have emergency response plans in place to handle contingencies that arise. The same can be said about waste disposal.
Document and Review
After making the appropriate changes, you can document the changes to ensure you have accurate records. Hold meetings with your employees to help everyone stay on the same page. Documenting this process can also help absolve you of blame in the future if legal issues arise.
How Often Should I Assess Risk?
In general, it’s recommended to conduct a chemical risk assessment at least once per year. However, there are certain scenarios where doing so more frequently would be appropriate. Let’s explore some of the most notable.
The Addition of New Employees
Adding new employees to your roster can change the overall workflow of your organization. By extension, this could impact the way your workers handle chemicals. A chemical risk assessment will help you determine areas of concern and allow you to make the appropriate changes.
Using New Equipment
With new equipment comes new responsibilities. Similar to the above scenario, adding new equipment to your company could inadvertently increase your overall workplace risk. This situation isn’t quite as common, as new equipment often doesn’t impact how your workers interact with chemicals.
Adding New Chemicals
Using new industrial chemicals could drastically increase the chance of a chemical reaction occurring. The chemicals could also be inherently dangerous and difficult to work with. Even if you add a single chemical to your roster, conduct a risk assessment.
You Use Volatile Chemicals
Chemical volatility is one of the most important factors to consider when assessing risk. It makes sense to conduct frequent tests if the chemicals used at your organization are more volatile than normal. All it takes is one oversight to result in disaster.
Your Industry Has Rigid Standards
Some industries have standards that eclipse those you’d find in other spaces. The pharmaceutical industry, for example, has more robust guidelines than the textile industry.
You’ll likely need to assess risk multiple times per year if your company operates in high-risk spaces. Stay updated on your industry’s regulations so you can make the most appropriate choice for your needs.
This will also help you avoid various issues, such as costly fines and fees. There’s something to be said about preventing damage to your company’s reputation, as well. People would be more likely to choose a competitor if your business becomes embroiled in controversy.
Getting Started
The more resources you use to identify and document risks, the easier it will be to manage them. Using online safety data sheets is a convenient and comprehensive way to handle your safety documentation.
When looking for resources, ensure you research their reputation. This plays a large role in finding the best opportunities and avoiding issues you may have otherwise encountered.
Never Neglect Your Chemical Risk Assessment
Although it might seem inconvenient at times, you must never neglect chemical risk assessment at your company. This could lead to numerous issues that could be virtually impossible to recover from. The good news is the tips in this guide will help ensure you get started on the right track.
KHA is proud to offer online access to safety materials that can help minimize risk at your facility. We’ve been a dedicated leader in safety data sheet management (SDS) since 1985 and will continue to go above and beyond for our clients. You’ll learn more about the many ways we can help when you schedule a call today.