How to Use Processes to Improve Safety in the Workplace
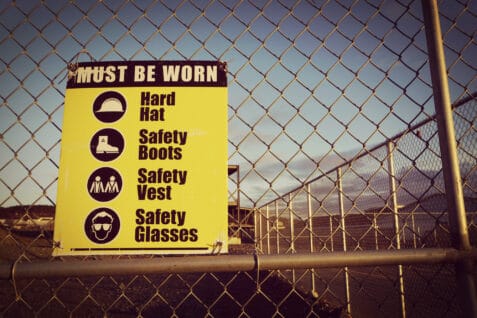
Two years ago, employers reported 2.6 million nonfatal workplace injuries and illnesses. While the numbers are lower than in earlier years, businesses can do better.
Safety in the workplace is a hot topic for employers today. A safe and healthy workplace protects workers from injury and illness. It increases productivity and helps raise employee morale.
Savvy managers rely on safety management systems to help reduce the risks of health hazards and workplace injuries. With the best processes in place, these systems can be highly effective.
In this article, we’ve included tips on how your team can use processes to enhance workplace safety.
What are Processes in the Workplace?
If you’ve followed directions, you’ve used a process. If the directions were clear, you maximized the likelihood of achieving a goal.
In the workplace, processes help people complete tasks, make decisions, and manage resources. Documentation is critical. Flowcharts, diagrams, and written instructions all work to document.
The overarching goal of safety management should be the improvement of your organization’s safety program. Most businesses carry this out through compliance, policies, and procedures. They also use processes.
Policies Procedures and Processes
Processes, procedures, and policies are guidelines. Businesses follow them to make sure they run effectively and safely. The problem with these three P’s is that people sometimes find it hard to tell when one starts and the other ends.
Here’s a high-level look at all three:
1. Processes – steps you need to take to complete a project
2. Procedures – set of instructions for completing a process
3. Policies – guidelines on how you should carry out processes and procedures
Effective safety management systems must include each of the above components. Documented and repeatable processes help employees do their jobs safely.
How Processes Improve Workplace Safety
Since organizations use processes to improve safety, you must know how you can help your company benefit from putting processes into place. In this section, we’ll focus on using processes to standardize procedures and identify hazards.
Standardizing Procedures
By standardizing procedures, organizations can ensure employees complete tasks in the same way—every time. When people are familiar with the required safety steps, they can proactively reduce errors and accidents.
For example, with hazardous materials processes in place, employees will know precisely what steps they need to take to handle those materials safely. Where there’s no process, employees will try to figure things out on their own. That could spell disaster.
Identifying Hazards
Data from the National Safety Council (NSC) shows that slip and trip accidents account for serious employee injuries resulting in days off from work. In 2020, these types of accidents caused 211,640 workplace injuries.
Assessing the work environment for health and safety hazards is necessary to prevent injuries and illnesses from happening. Here’s what a process to identify hazards might include:
- Conduct regular worksite inspections.
- Interview workers and managers.
- Create a hazard map
Your business can use processes to identify workplace hazards. Analyzing each step of a process means you can identify potential hazards and take steps to mitigate them.
Benefits of Using Processes to Enhance Workplace Safety
Implementing process safety can provide several benefits to organizations. One benefit is a reduction in accidents and workplace injuries.
Other benefits include the following
Protecting Workers and the Environment
Processes help to protect workers from exposure to hazardous materials and prevent damage to the environment. This can help organizations meet their regulatory requirements and avoid costly fines or legal action.
Increasing Productivity and Efficiency
By minimizing the risk of accidents and incidents, processes can help organizations maintain production schedules and avoid downtime. This can increase productivity and efficiency, and reduce the likelihood of delays or disruptions.
Improving Public Perception
Organizations that focus on process safety can enhance their reputation and improve their public perception. This can help to attract and keep customers, investors, and employees, and can also improve the organization’s brand.
Overall, implementing process safety can help organizations to create a safer, healthier, and more productive workplace, while also enhancing their reputation and brand.
Examples of Safety Process Failures
There have been several high-profile process safety failures in recent years. These failures resulted in health hazards and many workplace injuries. Some examples include:
BP Texas City Refinery Explosion
In 2005, an explosion at the BP Texas City refinery killed 15 people and injured more than 170 others. A combination of factors caused the incident, including inadequate safety measures, poor maintenance, and a failure to adequately assess and manage risks.
Deepwater Horizon Oil Spill
In 2010, an explosion on the Deepwater Horizon oil rig in the Gulf of Mexico resulted in the largest marine oil spill in history. A failure in the blowout preventer—designed to shut off the flow of oil in the event of an emergency—caused the spill.
Fukushima Nuclear Disaster
In 2011, a massive earthquake and tsunami in Japan caused a nuclear disaster at the Fukushima Daiichi power plant. The failure of multiple safety systems, including backup generators and cooling systems, caused the disaster. These failures led to reactor meltdowns and releases of radioactive materials.
These incidents highlight the importance of safety processes and the need for organizations to take proactive measures to prevent similar failures in the future.
Processes and Employee Training
Employees, particularly new employees, aren’t always aware of the risks associated with the tasks they must complete during their workday.
Documenting processes is an excellent training tool. When you give clear, step-by-step instructions, employees can feel confident about safely completing tasks.
Another benefit of using processes in the workplace is that all employees receive the same training. This helps an organization maintain consistency, which minimizes the likelihood of errors.
Training is an ongoing activity for most organizations. It’s the only way for businesses and their employees to keep up with changes in their particular industries.
With training, comes many opportunities for employee growth and improvement. Improvement should be a continuous focus in the area of workplace safety, and processes help. Next, we’ll show you how.
Assessing and Analyzing Processes for Continuous Improvement
Any organization can use processes to improve workplace safety. Monitoring processes and analyzing safety data help target areas where you can improve. We owe it to our team members, customers, patients, and shareholders.
One way to do this is to break it down into the following three phases:
Assessment
During the first part of the assessment, focus on gathering data. Find both good and bad processes. When you identify processes that are working, consider those as best practices.
This phase is for recognizing what’s working and what isn’t. You’ll also spend time gathering and analyzing data.
Problem-Solving
Activity during this phase should include coming up with the most valuable solutions—getting the biggest bang for your buck.
This phase takes time as you’ll need to get down to the roots of the process problems rather than focusing on what you can only see at the surface level.
Implementation
In this phase, it’s time to apply changes. Implementation is both exciting and frustrating. It will require team members to adapt, which is often challenging for most, if not all, employees.
A Real Life Example
If you’re new to using processes as a method of working toward continuous improvement, it can be difficult to picture how it could work for your organization.
Here’s an example of how process improvement might work for an emergency response team where the potential for exposure to biological hazards is high.
Biological hazards include blood, urine, feces, bacteria, and viruses.
If safety data shows that staff experiences frequent health issues due to contact with bodily fluids or bacteria and viruses, management will first recognize processes that are working.
After identifying processes that aren’t working, safety management staff should brainstorm. Brainstorm sessions include management and staff.
Next, the team comes up with solutions, a.k.a., problem-solving.
Maybe employees aren’t taking enough time to stock sterile gloves and protective gear, which puts them at a higher risk for contact with bio-hazards. Or perhaps the team includes new employees who need extra time for training.
It’s time to put new processes in place, remembering to check and analyze new data to ensure there is a continuous trajectory of improvement.
Challenges in Implementing Safety Processes
All organizations face challenges anytime they try to introduce new safety processes. It’s critical to anticipate challenges and develop strategies to overcome them. Unless you know the reason behind the challenge, it will be nearly impossible to develop good strategies that encourage staff buy-in.
Here are several reasons why your staff may resist your attempts to make changes to processes.
Resistance to Change
One of the main challenges organizations face when introducing new safety processes is getting buy-in from employees and management. People are often resistant to change and may feel that new safety processes are unnecessary or burdensome.
Insufficient Resources
Implementing new safety processes may require significant investment in time, money, and resources. Organizations may feel hesitant to allocate these resources, particularly if they are already stretched thin.
Lack of Understanding and Awareness
Employees and management may not fully understand the new safety processes, which can lead to confusion, mistakes, and non-compliance.
Over-Reliance on Technology
Some organizations may rely too heavily on technology to improve safety processes, without adequately considering human factors or organizational culture.
Ineffective Communication
Clear communication is essential for implementing new safety processes. If communication is unclear, inconsistent, or insufficient, employees may not understand the importance of the new processes or how to follow them.
Inadequate Training
Employees may not have the necessary skills or knowledge to effectively implement the new safety processes. Without proper training, the new processes may not be effective.
Be aware of potential challenges before moving your organization into the implementation phase, and you stand a much better chance of successfully launching new safety processes.
How to Help Employees Adapt to Processes
Getting employees on board with safety processes is essential for maintaining a safe workplace. Here are some steps you can take to help your staff adapt to new safety processes:
- Communicate the importance of safety
- Explain the risks
- Provide proper training
- Make processes easy to follow
- Encourage feedback
- Reward safe behavior
- Lead by example
Overall, getting staff buy-in on safety processes requires clear communication, proper training, and a culture that values safety. By taking these steps, you can help ensure a safe workplace for all staff.
Review and Update Processes
All the work done to target problems, develop processes, and design effective training programs won’t be done unless safety managers take the time to review and update processes.
First, processes must be up-to-date. This might involve reviewing safety incidents and identifying issues.
Your organization may need to buy new equipment to help employees do their jobs safely. In that case, you’ll need to create and/or update processes on using the new equipment.
Using safety data sheets (SDS) is one vital resource your organization can use to review and analyze data in order to update processes.
Remember that organizations cannot take safety for granted. Regular assessment and evaluation is the key to a safe workplace.
We Can Help You Improve Safety in the Workplace
Given the benefits of implementing process safety, organizations need to take proactive steps to find and control potential hazards in the workplace.
To ensure the safety of their employees and protect the environment, organizations must prioritize process safety and develop effective safety management systems.
Kelleher, Helmrich, and Associates, Inc. (KHA) specializes in helping businesses improve safety in the workplace by providing Safety Data Sheet (SDS) Management. Contact us today to learn more about how we can help your organization.