The Latest Strategies for Accurate Chemical Inventory Management
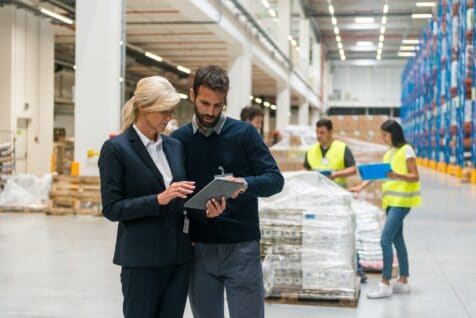
For businesses that work with chemicals, precision holds the key to chemical safety and compliance. Imagine a subtle miscalculation jeopardizing not just your operations but also the well-being of those involved. From research labs to industrial facilities, the importance of accurate chemical inventory management is paramount.
This article unveils the latest strategies in chemical inventory management, illuminating the pathways towards utmost precision and safety. Read this article to discover how industry leaders are mitigating risks when it comes to hazmat inventory.
You’ll learn how to safeguard personnel and fortify your bottom lines through a renewed focus on accuracy and compliance with hazmat regulations.
Stay with us as we dive into the world of chemical inventory management, where accuracy becomes the keystone for a safer, more efficient, and compliant future.
The Consequences of Inaccurate Chemical Inventory Management
Accurate chemical inventory management is far more than a mundane administrative task. It’s the cornerstone of operational safety and success in a chemical-intensive world.
The consequences of inaccurate inventory management extend far beyond mere record-keeping errors.
Safety Hazards
Inaccurate chemical inventories can transform the workplace into a potential minefield. A slight mix-up of chemicals or an absence of critical safety data can lead to hazardous situations.
Accidental spills, incompatible chemical reactions, and improper handling of substances become all too likely when inventories are not kept up to date. The consequences can range from minor incidents to catastrophic accidents that endanger lives and the environment.
Compliance Issues
Regulatory bodies at the local, national, and international levels impose strict rules and standards for chemical handling and reporting.
Failure to maintain accurate inventories can result in non-compliance, leading to fines, legal troubles, and a tarnished reputation. The cost of non-compliance often surpasses the investment required for proper inventory management.
Financial Losses
Inaccurate chemical inventories can be financially crippling. Overstocking chemicals due to inaccurate records leads to unnecessary spending.
Understocking can halt operations, resulting in lost productivity and revenue.
Emergency purchases to compensate for shortages come at a premium. Inefficiencies and waste add up. This impacts the bottom line significantly.
Regulatory and Compliance Considerations
The regulatory landscape governing chemical inventory management varies by country, region, and industry. In the United States, the Occupational Safety and Health Administration (OSHA) sets forth regulations that govern chemical hazard communication through the Hazard Communication Standard (HCS).
Under HCS, organizations are required to maintain accurate records of all hazardous chemicals in the workplace. This includes details on their composition, potential hazards, and safe handling procedures.
The Globally Harmonized System of Classification and Labeling of Chemicals (GHS) is an internationally recognized framework. It standardizes chemical labeling and safety data sheets across borders and deals with a wide range of hazmat safety issues.
Beyond these standards, other countries have their own specific regulations. This makes it crucial for organizations to stay updated on the requirements applicable to their operations. Failure to comply can result in a myriad of serious consequences.
Legal Repercussions
Non-compliance with chemical inventory regulations can lead to severe legal repercussions. Organizations may face fines or even legal action.
Fines can vary widely. They often depend on the severity of the violation, the potential harm it poses, and the size of the organization.
In some cases, non-compliance may even result in criminal charges if willful negligence or intent is proven.
Financial Consequences
Financial losses due to non-compliance are not limited to fines and penalties. They extend to a range of indirect costs that can cripple a business. These include downtime caused by:
- Investigations
- Legal fees
- Reputation damage
- Shutdowns or production halts
Emergency corrective actions, such as the recall of non-compliant products or the remediation of contaminated sites, can impose significant financial burdens.
Furthermore, the long-term financial viability of a company can be threatened as customers may prefer to work with compliant suppliers to minimize their own risks. Non-compliance can lead to loss of business, decreased market share, and erosion of trust among clients and stakeholders.
Modern Technologies for Chemical Inventory Management
These technologies, such as inventory management software, RFID tagging, and IoT sensors, are enhancing accuracy and efficiency while significantly impacting the overall safety of these crucial operations.
Let’s take a closer look at them.
Inventory Management Software
Inventory management software is a game-changer in the realm of chemical inventory management. These advanced software solutions provide real-time data. They enable organizations to have an up-to-the-minute view of their chemical stocks. This real-time information is invaluable for decision-making and compliance.
Inventory management software often incorporates barcoding and QR codes for labeling containers, making it easy to scan and update inventory levels. This reduces the margin of error associated with manual data entry.
Many software solutions offer a chemical compatibility check feature, helping to prevent hazardous chemical combinations and ensuring a safer workplace.
These features result in enhanced accuracy and efficiency as organizations maintain up-to-date records and reduce the risk of errors. This is all done while ensuring compliance with regulatory standards.
RFID Tagging
Radio-frequency identification (RFID) tagging is yet another transformative technology in chemical inventory management. RFID tags are affixed to chemical containers and can be scanned remotely using RFID readers. This automation significantly reduces the need for manual data entry, minimizing human error and accelerating the inventory process.
RFID enables real-time tracking of chemical movements within a facility, particularly useful in large warehouses or facilities with a high volume of chemical traffic. Security is also bolstered by RFID technology, as it allows for access control-only authorized personnel with RFID readers can access specific chemical storage areas.
As a result, RFID tagging enhances the accuracy and efficiency of chemical inventory management by enabling swift tracking, reducing data entry errors, and improving security measures.
IoT Sensors
The Internet of Things (IoT) has brought about new possibilities for chemical inventory management through a network of sensors and devices that communicate and share data.
These IoT sensors can monitor environmental conditions, such as temperature, humidity, and air quality, which are critical for chemicals with specific storage requirements. Moreover, IoT sensors can provide predictive maintenance alerts, reducing the risk of leaks or spills due to equipment failure.
They can also send alerts and notifications to responsible personnel when certain conditions are met, such as low chemical levels or environmental deviations. Furthermore, IoT technology enables data analysis, which can be used to make informed decisions, optimize storage, and enhance safety.
The integration of IoT sensors results in highly accurate chemical inventory management, offering real-time monitoring, predictive capabilities, proactive maintenance, and a reduced risk of incidents, ultimately improving overall efficiency.
Data Accuracy in Chemical Inventory Management
Accurate data capture and tracking lies at the heart of effective chemical inventory management. The precision with which data is collected and maintained can be the difference between a safe and compliant operation and one fraught with risks and regulatory challenges.
The Critical Importance of Data Accuracy
Accurate data capture is fundamental in chemical inventory management for several reasons. First and foremost, it is a vital component of regulatory compliance.
Accurate records of chemical inventory are essential for meeting regulatory requirements, as numerous standards mandate the detailed tracking of chemical usage, storage, and disposal. Organizations failing to maintain accurate records may find themselves in non-compliance, exposing them to legal and financial risks.
Moreover, accurate data capture is integral to safety. It helps in identifying and mitigating potential hazards, ensuring that chemicals are stored, handled, and used in ways that minimize risks to personnel and the environment.
Inaccurate data can lead to dangerous situations, such as incompatible chemicals being stored near each other, increasing the risk of chemical reactions and accidents.
The Role of Safety Data Sheets (SDS)
Safety Data Sheets (SDS) are a cornerstone of chemical inventory management, providing detailed information about the properties, hazards, and safe use of chemicals. SDS sheets contain vital data such as chemical composition, physical and chemical properties, health hazards, and safety precautions.
Accurate and up-to-date SDS sheets are crucial for worker safety, emergency response, and regulatory compliance.
SDS sheets are not only a source of information but also a regulatory requirement in many jurisdictions. They are used to educate workers about the risks associated with specific chemicals and provide guidance on proper handling, storage, and disposal. Accurate SDS sheets ensure that workers are well-informed and can take the necessary precautions to avoid accidents and injuries.
Technological Advancements for Enhanced Data Accuracy
Technological advancements have significantly improved data accuracy and tracking in chemical inventory management. Among these, barcoding, mobile apps, and cloud-based systems have played pivotal roles.
Barcoding
Barcoding is a simple yet powerful tool for improving data accuracy. Each chemical container is assigned a unique barcode that can be quickly scanned, ensuring accurate identification and tracking.
When a chemical is used or restocked, scanning the barcode updates the inventory in real-time, reducing the risk of manual entry errors. Barcoding not only enhances accuracy but also saves time, making inventory management more efficient.
Mobile Apps
Mobile applications designed for chemical inventory management allow personnel to record data at the point of use. Employees can use smartphones or tablets to scan barcodes, update quantities, and access SDS sheets on the spot.
This real-time data capture ensures that the inventory remains accurate, and it promotes compliance by enabling immediate access to safety information when needed.
Cloud-Based Systems
Cloud-based inventory management systems offer secure and centralized data storage. This technology ensures that data is consistently updated across all devices and locations within an organization. Real-time access to data, including SDS sheets, is readily available to authorized personnel, regardless of their physical location.
Cloud-based systems provide the flexibility to scale operations as needed, accommodating the dynamic nature of chemical inventory management.
Risk Mitigation and Safety Protocols
Accurate chemical inventory management serves as the linchpin for better risk mitigation and the enhancement of safety protocols in organizations dealing with chemical substances.
By maintaining precise and up-to-date records of their chemical inventory, businesses can significantly reduce the risk of accidents, emergencies, and regulatory non-compliance.
Hazard Identification
Accurate inventories provide essential information about the types and quantities of chemicals on-site. This knowledge is fundamental for identifying potential hazards and assessing associated risks.
For instance, if incompatible chemicals are stored close together due to inaccurate records, the risk of chemical reactions and dangerous incidents increases.
Preventing Overstocking and Understocking
Accurate inventories help organizations avoid overstocking, which can lead to the unnecessary storage of hazardous materials, and understocking, which can result in emergency orders and potential disruptions.
Both of these situations can increase safety risks and operational inefficiencies.
Regulatory Compliance
Maintaining precise chemical inventories is a regulatory requirement in many industries. Non-compliance with these requirements can lead to legal issues and fines.
Inventory accuracy is a fundamental aspect of compliance with safety regulations.
Emergency Preparedness
Accurate chemical inventories are crucial in emergency preparedness and response. In the event of a chemical spill, fire, or other emergency, first responders need precise information about the substances involved, their hazards, and appropriate response measures.
Inaccurate records can impede emergency response efforts and increase the severity of the incident.
Examples of Improved Safety
Numerous organizations have realized tangible safety improvements by prioritizing accurate chemical inventory management. Here are a few notable examples.
Pharmaceutical Manufacturers
Companies in the pharmaceutical industry have achieved heightened safety levels by accurately tracking their chemical inventories.
By ensuring that chemicals are stored in accordance with safety guidelines and by promptly replacing or disposing of expired or unstable compounds, they’ve mitigated the risk of unforeseen chemical reactions that could compromise product quality and worker safety.
Research Laboratories
Research facilities, often dealing with a diverse range of chemicals, have significantly improved safety through precise inventory management.
Accurate records allow researchers to quickly identify and remove chemicals that may have become unstable or hazardous over time, reducing the risk of accidents and exposures.
Industrial Plants
Industrial plants with complex chemical processes have embraced accurate inventory management to maintain safe operations.
By accurately tracking chemicals used in various processes and ensuring their correct storage, these plants have reduced the likelihood of accidents, emissions, and operational disruptions.
Emergency Response Teams
Fire departments and emergency response teams rely on accurate chemical inventories when dealing with chemical incidents.
Detailed records help these teams understand the risks, select appropriate protective measures, and manage the response effectively.
Inventory Auditing and Reconciliation
Regular inventory auditing and reconciliation are vital processes in an effective chemical inventory system.
These systematic procedures serve to maintain data accuracy, identify discrepancies, and ensure compliance with regulatory standards.
Scheduling Audits
Organizations should establish a routine schedule for inventory audits and reconciliations.
The frequency can vary depending on factors such as the volume of chemical inventory, regulatory requirements, and industry standards.
Preparation
Preparation is crucial. Gather all necessary documentation, including chemical records, Safety Data Sheets (SDS), and any relevant regulatory guidelines.
Ensure that the audit team is well-prepared and equipped with the necessary tools, such as inventory management software, barcoding devices, and safety equipment.
Physical Verification
A comprehensive audit begins with a thorough physical inspection of the chemical inventory.
This involves verifying the presence, condition, and quantities of each chemical, and cross-referencing them with the corresponding entries in the inventory management system.
Documentation Review
Concurrently, review the accuracy of the chemical documentation, including SDS sheets, labeling, and any updates required by regulatory authorities.
It’s imperative that all records are up-to-date and aligned with the physical inventory.
Discrepancy Identification
During the audit, any discrepancies discovered should be documented and investigated. Discrepancies can encompass missing chemicals, incorrect quantities, or expired substances.
Each discrepancy should be meticulously reviewed, and corrective actions should be initiated, focusing on identifying the root causes of discrepancies.
Reconciliation
Following the audit, a crucial step is to reconcile the physical inventory with the electronic records, adjusting the records to match the actual quantities and conditions of the chemicals.
Reconciliation is a pivotal step to ensure that the inventory database accurately reflects the real-world inventory.
Compliance Verification
As an integral part of the audit process, organizations must ensure that the chemical inventory complies with all relevant regulatory requirements, such as labeling, storage, and disposal.
Non-compliance issues should be addressed promptly to prevent potential violations.
Reporting
To document the audit findings and outcomes, generate a comprehensive audit report. This report should summarize the findings, discrepancies identified, corrective actions taken, and any compliance concerns.
Additionally, it should provide recommendations for improving inventory management processes.
Continuous Improvement
Utilize the audit findings to implement continuous improvement measures. Address any systemic issues contributing to discrepancies and revise standard operating procedures to prevent future inaccuracies.
Benefits of Inventory Auditing and Reconciliation
By conducting regular audits and reconciliations, organizations not only meet regulatory requirements but also reinforce their operational integrity and reliability.
These practices are a fundamental aspect of a robust chemical inventory management strategy, contributing to the safety and success of organizations dealing with chemical substances.
Data Accuracy
Regular audits and reconciliations significantly enhance data accuracy.
By identifying and rectifying discrepancies, organizations ensure that their chemical inventory database precisely mirrors the actual state of the inventory.
Regulatory Compliance
Auditing guarantees that the chemical inventory adheres to all relevant regulatory standards. This reduces the risk of non-compliance issues, which could result in fines and legal consequences.
Hazard Mitigation
Identifying discrepancies and non-compliance issues through audits enables proactive hazard mitigation. This reduces the risk of accidents and chemical reactions arising from improper storage or handling.
Operational Efficiency
Accurate chemical inventories promote operational efficiency by allowing organizations to avoid overstocking, reduce costs linked to unnecessary chemical purchases, and optimize storage space.
Enhanced Safety
Auditing and reconciliation significantly enhance workplace safety.
By ensuring that the inventory accurately reflects the presence of hazardous substances, the risk of accidents and exposures is reduced, contributing to a safer working environment.
Supplier and Procurement Integration
The seamless integration of suppliers and procurement processes is a strategic move that can significantly enhance the accuracy of chemical inventory management.
In today’s interconnected business landscape, effective communication and collaboration with suppliers are paramount.
Real-Time Data Exchange
Integrating suppliers into your chemical inventory management system enables real-time data exchange.
This means that as suppliers deliver chemicals or update product information, the inventory management system is updated automatically. This leads to more accurate and up-to-date inventory records.
Reducing Data Entry Errors
Manual data entry errors are a common source of inaccuracies in inventory records. By integrating suppliers and procurement processes, you minimize the need for manual data entry, reducing the risk of typographical errors and inaccuracies.
Automatic Inventory Updates
When a shipment of chemicals arrives, the integration allows the inventory system to automatically update the quantities and details, ensuring that the records accurately reflect the newly acquired chemicals.
Strategies for Improved Communication and Tracking
The ability to receive real-time updates and reduce manual data entry errors is instrumental in achieving a more precise and efficient chemical inventory management system.
Electronic Data Interchange (EDI)
Implement an Electronic Data Interchange system to facilitate seamless communication with suppliers. EDI allows for the electronic exchange of documents, such as purchase orders and invoices, reducing the reliance on paper-based communication and the risk of transcription errors.
Supplier Portal
Create a dedicated supplier portal that provides suppliers with access to submit information about chemical deliveries and updates directly into your inventory management system. This self-service portal ensures that the most accurate and up-to-date information is entered directly.
Barcoding and RFID
Implement barcoding and RFID tagging on chemical containers upon arrival. This technology enables you to scan incoming chemicals, immediately updating the inventory with accurate information.
Regular Supplier Audits
Conduct regular audits of your suppliers to ensure they adhere to agreed-upon communication and data standards. This helps maintain consistency in data accuracy.
Automated Alerts
Utilize automated alerts and notifications in your inventory management system to inform relevant personnel when new chemicals arrive or when any discrepancies are detected. Prompt notifications ensure that discrepancies are addressed immediately.
Improve Your Company’s Chemical Inventory Management Today
As an industry leader, KHA has seen firsthand the transformative power of precision in inventory records. From regulatory compliance to safety enhancement, the benefits are manifold. We offer cutting-edge solutions and expert guidance to help organizations streamline their chemical inventory management practices.
Elevate your operations, mitigate risks, and safeguard your workforce and environment. Contact KHA today for a consultation and take the first step toward a safer and more efficient future.