What is an SDS? Unveiling the Safety Data Essentials
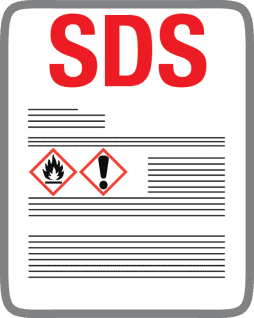
Millions of workers unknowingly face hazardous chemical exposure daily in their workplaces. TDI Texas reports that the Occupational Safety and Health Administration (OSHA) estimates that over 32 million workers in 3.5 million workplaces encounter dangerous substances regularly. Without the right safety measures in place, these exposures can lead to severe health risks and legal consequences.
Understanding what is an SDS and how it functions is essential for businesses handling chemicals. Safety Data Sheets (SDS) provide vital information about hazardous substances, equipping employees with the knowledge to prevent accidents.
Keep reading to discover how SDSs can protect your employees and streamline chemical safety in your organization.
Understanding Safety Data Sheets (SDS)
What is an SDS? An SDS, formerly known as a Material Safety Data Sheet (MSDS), is a document that provides detailed information about a chemical substance.
It is a critical resource for businesses handling hazardous materials, ensuring employees are aware of potential risks. Compliance with SDS regulations is essential for maintaining a safe and legally compliant workplace.
An SDS outlines the following:
- Chemical’s properties
- Associated hazards
- Safe handling practices
- Emergency control measures
The primary purpose of an SDS is to inform and protect those who handle, transport, or are exposed to hazardous chemicals in the workplace.
Why Are SDSs Important?
Workplace safety hinges on effective communication about potential hazards. Safety Data Sheets serve as the cornerstone of this communication by offering comprehensive details that enable employers and employees to make informed decisions regarding chemical safety.
SDSs are essential for the following reasons:
- Hazard identification: Describes the dangers associated with a chemical, including health risks and environmental impacts
- Preventive measures: Provides guidelines on safe handling, storage, and disposal to minimize risk
- Emergency procedures: Outlines steps to take in case of accidental exposure, spills, or fires
- Regulatory compliance: Ensures businesses meet OSHA’s Hazard Communication Standard (HCS) requirements
- Employee safety training: Helps educate workers about proper handling and risk mitigation
OSHA’s Hazard Communication Standard (HCS)
OSHA’s Hazard Communication Standard (HCS) mandates that employers develop a written hazard communication program. This includes maintaining Safety Data Sheets for all hazardous chemicals in the workplace. The program ensures that employees have access to vital information about the chemicals they may encounter.
According to OSHA’s Hazard Communication Standard (HCS) 29 CFR 1910.1200, all employers must:
- Maintain a readily accessible SDS for every hazardous chemical used in the workplace
- Train employees on how to read and understand SDSs
- Ensure proper labeling of all hazardous chemicals
- Implement procedures for handling hazardous substances safely
Failure to comply with these regulations can result in significant fines and increased workplace risks.
Structure and Content of an SDS
An SDS follows a standardized 16-section format, as outlined by the Globally Harmonized System (GHS) of Classification and Labeling of Chemicals. This uniform structure ensures that all relevant safety information is easily accessible and consistently formatted across industries.
Each SDS provides essential details about a chemical’s properties, potential hazards, and the necessary precautions to handle and store it safely.
Regulatory bodies such as OSHA and the Globally Harmonized System (GHS) mandate their use, reinforcing their importance in workplace safety. Understanding how to interpret and implement these guidelines is fundamental for businesses aiming to maintain compliance and ensure worker safety.
Implementing Effective SDS Management
Proper SDS management is vital for maintaining compliance and ensuring employee safety. Without a structured approach, outdated or missing SDSs can lead to regulatory violations and increased workplace hazards. Key strategies include:
- Accessible storage: Ensure that Safety Data Sheets are readily accessible to all employees during their work shifts
- Regular updates: Keep SDSs current by obtaining the latest versions from manufacturers or suppliers
- Employee training: Educate staff on how to read and interpret SDSs, emphasizing the importance of the information provided
- Utilizing technology: Implement SDS mobile apps and online SDS platforms to streamline access and management
Advantages of SDS Mobile Apps and Online SDS Platforms
Technology has revolutionized the way businesses handle safety compliance. Digital solutions make it easier to access, update, and share critical safety information in real time.
Incorporating technology into SDS management offers numerous benefits, such as:
- Instant access: SDS mobile apps allow employees to retrieve safety information on the go
- Centralized database: Online SDS platforms provide a centralized repository
- Regulatory compliance: Automated tracking and notifications help maintain compliance with OSHA regulations
- Environmental impact: Reducing paper usage aligns with sustainability initiatives
The Future of SDS Management
Advancements in technology are making SDS management more efficient than ever. Companies are moving toward cloud-based SDS solutions by offering:
- Real-time updates
- Improved security
- Seamless integration with other safety management systems
Features such as barcode scanning and AI-powered search functions enhance the user experience. This makes it easier to locate crucial chemical safety information within seconds.
Organizations that adopt SDS mobile apps and online SDS solutions not only improve their safety protocols but also demonstrate a commitment to employee well-being and regulatory compliance. As regulatory bodies continue to refine hazard communication standards, businesses must stay proactive in managing their chemical safety documentation.
KHA’s Expertise in SDS Management Solutions
KHA, headquartered in Merrillville, Indiana, has been a leader in SDS management since 1985. We offer a suite of services designed to enhance workplace safety and compliance, including:
- Online-SDS™: A cloud-based solution providing unlimited access to a vast database of Safety Data Sheets
- SDS-Mobile: A mobile app that allows users to access their chemical inventory and SDSs from any device, ensuring information is always at their fingertips
- HazMat Inventory Integration: Links SDSs with a company’s hazardous material inventory, improving safety and compliance
What Is an SDS and Why Should You Take Action?
Understanding what is an SDS is essential for any organization dealing with hazardous chemicals. Proper SDS management is crucial in maintaining workplace safety, reducing risk, and ensuring regulatory compliance. With SDS mobile apps and online SDS platforms, businesses can improve accessibility, streamline compliance, and protect their employees from potential hazards.
KHA provides award-winning SDS management solutions trusted by thousands of organizations across multiple industries. KHA’s expertise ensures businesses have access to cutting-edge SDS services tailored to their safety needs.
Schedule a demo today to discover how KHA’s solutions can enhance your organization’s chemical safety program and compliance efforts.